The Difference Between Densifiers and Sealers
A beautifully finished decorative concrete floor must go through a fairly involved process to achieve the intended outcome. From the “pure” pour through the glossy finish, concrete needs to be chemically altered before a floor is ready for prime time. Densifiers and sealers are applied to decorative concrete flooring at different stages and serve different purposes.
The Building Blocks of Concrete
Portland cement is the basic ingredient of concrete. Concrete is formed when portland cement is combined with water. Cement and water form a paste that coats and binds with sand and rock. Through a chemical reaction called hydration, the paste hardens and gains strength to form the rock-like mass known as concrete.
The longer the concrete is kept moist, the stronger and more durable it will become. The rate of hardening depends upon the composition and fineness of the cement, the mix proportions, and the moisture and temperature conditions. Concrete continues to get stronger as it gets older. Most of the hydration and strength gain take place within the first month of concrete’s life cycle, but hydration continues at a slower rate for many years.
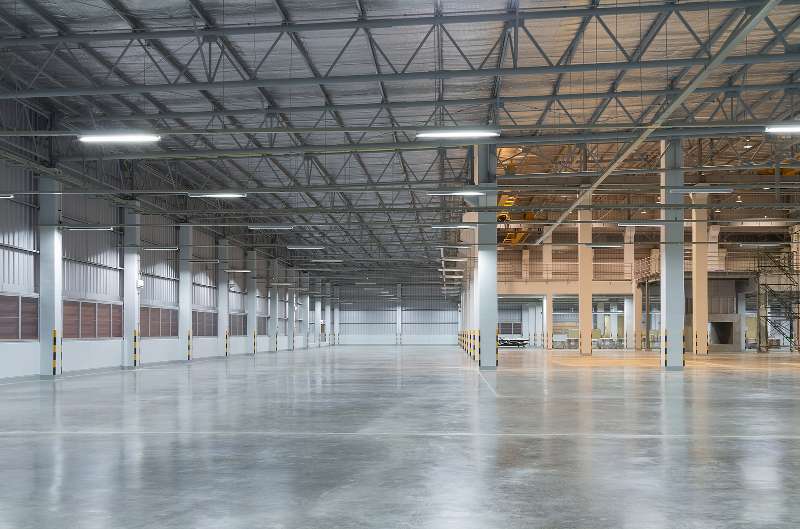
Densifiers: Chemically Hardening Concrete Flooring
Calcium Hydroxide is left over from the cement paste hydration process. If left untreated, calcium hydroxide reacts with carbon dioxide in the air and turns into chalky dust. Dust ends up on everything.
For years, the only remedy to sealing concrete floors was to cover them with a film or membrane. Products included acrylics, urethanes, epoxies and waxes. These treatments were a temporary method of sealing concrete. They are subject to delamination, scratching, chipping and wear. Eventually, they have to be replaced.
Densification – Hardening From the Inside Out
A concrete floor is usually between 4-6” inches thick. Most of the wear takes place in the top 1/16th inch wear zone of the concrete. That’s where the concrete is most vulnerable. Densification is not a topical layer that seals the surface of a concrete floor. Densification is the application of a liquid silicate hardener to a concrete surface to create a chemical reaction. The densification reaction process fills in the natural pores and voids in the concrete through a process of crystalline growth. The concrete is densified internally and inorganically. The same reaction also hardens the concrete and locks up the dust.
What remains is a crystalline-densified version of the concrete that was there in the first place. Because the chemistry is inorganic, there is nothing to wear out, scratch or peel. The seal is the result of an ongoing chemical reaction that takes several months to complete.
Once densification takes place, foreign matter such as oil, alkali, free lime and traffic scum are easily removed with regular cleaning. A regular maintenance program is highly recommended to remove surface contaminants. Any acids or other corrosive materials should be removed immediately from the floor.
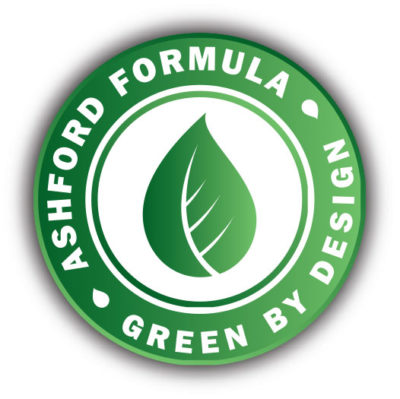
Ashford Formula – LEED Certified Densifier
Ashford Formula is a chemically reactive densification liquid that penetrates the concrete, solidifying the concrete surface components into a solid mass. It produces a permanently denser, harder, penetration and abrasion-resistant concrete surface. Ashford Formula is inorganic, non-toxic, VOC free, colorless and odorless. It produces no fumes, vapors, off-gassing and improves indoor air quality.
- The Ashford Formula’s green qualities make it an exceptional choice for today’s sustainable and green building initiatives. It has been widely specified for use on projects that have garnered LEED Certified, LEED Silver, LEED Gold and LEED Platinum status.
- An Ashford Formula treated floor will be 32% harder within the first 30 minutes of treatment. The treated concrete will continue to harden over time. The Ashford Formula also acts as a supplement to surface and aggregate hardeners. also significantly reduces crazing, or “map cracking” because it stabilizes the surface.
- Floors are more resistant to staining, easier to clean, and free from dusting. In our experience, densifiers also produce a higher, deeper gloss.
Immediately After Treatment
- The hardening and dust proofing will take effect within the normal curing period on new concrete and within 24-48 hours on existing concrete. The floor will have a normal concrete appearance or a slight sheen (broom-finished or rough-textured concrete will retain its natural concrete appearance.)
- The density and hardness of the floor will be immediately enhanced. However, care should be taken not to gouge the floor with nails, etc. after the initial placement.
- To accelerate the sheen, the floor can be burnished or cleaned daily using an auto-scrubber equipped with medium-aggressive nylon brushes. A spiff coat can also be done to enhance the initial sheen.
3-6 Months After Treatment
- If the standard maintenance program is followed, smooth-troweled floor surfaces will develop a sheen.
- Note: A sheen will not develop on floors with an open, porous finish, or on floors with a broom finish.
- On steel-troweled floors, water typically begins to bead on the surface.
12 Months After Treatment
- A hard shell-finished surface will develop.
- Surface is resistant to oil penetration and moisture contamination.
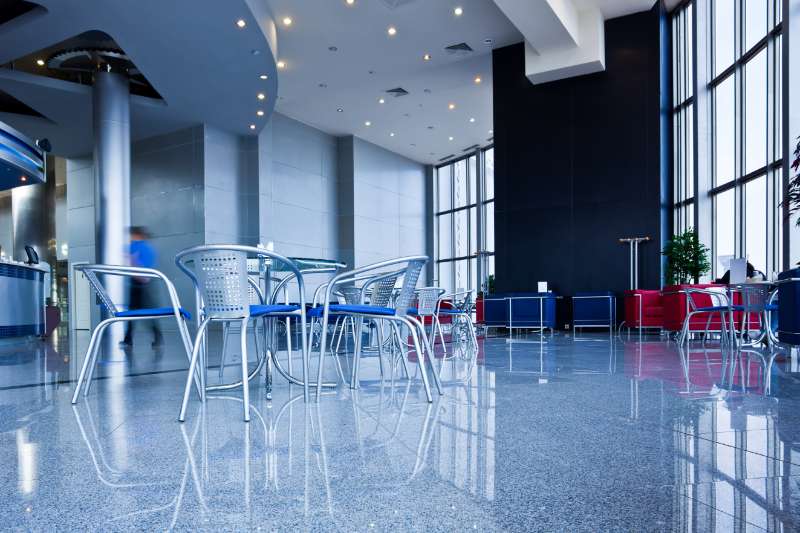
Sealers
When a decorative application to a concrete floor is nearing completion, after the color (if applicable) and densifier have been applied, a sealer is applied as the final step. A sealer brings out the beauty of decorative concrete flooring by enhancing the color and the sheen. A sealant also protects the floor surface from abrasions and stains. Depending upon the sealer, a floor may require additional applications of a sealer.
Sealer Types (from Concrete Network)
Acrylics
- Available in both solvent- and water-based formulations.
- Acrylic sealers form a thin, protective film that provides good protection against water and chloride intrusion while permitting moisture in the slab to escape.
- Acrylic sealers are UV resistant and non-yellowing.
- Water-based sealers are low VOC.
- Solvent-based acrylics generally perform better than water-based products for outdoor use.
- Softer acrylic sealers usually require regular maintenance with several coats of a sacrificial floor finish, or wax, to prevent wear and black heel marks.
- Available in a range of sheen levels, they also can be used to enhance the beauty of colored, stamped or exposed-aggregate concrete.
- Acrylic sealers usually wear faster than polyurethanes and epoxies.
Epoxies
- Epoxy sealers are much harder than acrylics.
- Epoxy sealers form a high-build protective film on the concrete surface, producing a hard, long-wearing, abrasion-resistant finish.
- Water-based epoxies bond well to concrete and provide a clear finish, but they are nonporous and do not allow trapped moisture to escape.
- They are highly water repellant.
- Epoxies are available clear or pigmented, if you wish to add color.
- Most products impart a glossy finish.
- Epoxies are ideal for food-preparation areas.
Polyurethanes
- Nearly twice as thick as acrylic sealers, and produce a very durable chemical- and abrasion-resistant finish.
- They can be used on both interior and exterior concrete to impart a transparent, non-yellowing, highly durable finish.
- Most urethanes are moisture intolerant until they cure, so no water should be present on the surface when the sealer is applied.
- Best uses include:
- Floors in high-traffic areas, to provide good resistance to scuffs and staining
- To enhance the beauty of colored, stamped or exposed-aggregate concrete
- Concrete countertops
Penetrating Sealers
Includes silanes, siloxanes, silicates, and siliconates
- Best used for outdoor concrete. Provide excellent protection against outdoor exposure conditions. Most products are also breathable, allowing moisture vapor to escape.
- Protect exterior concrete surfaces subject to corrosion and freeze-thaw damage.
- Obtain a natural, matte finish.
- Provide invisible protection without changing the surface appearance or leaving a sheen.
- Because a penetrating sealer does not leave a glossy film, it will not contribute to the slipperiness of the concrete surface.
Sealers for Polished Concrete
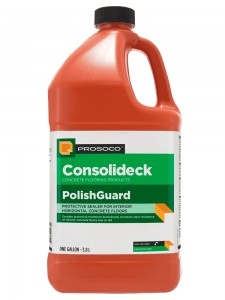
Consolideck® PolishGuard
Consolideck® PolishGuard is a durable, chemical-resistant, high-gloss, protective coating that dramatically increases the stain resistance of interior concrete floors. PolishGuard is ideal for steel-troweled, burnished, polished or decorative concrete and cement terrazzo floors that are exposed to accidental spills of food products, household cleaners and industrial solutions.
- Produces a long-lasting, tough protective shine on any interior concrete flatwork.
- Perfect for floors hardened/densified with Consolideck® LS® and LS/CS®.
- Adds depth and luster to colored concrete, including surfaces decorated with Consolideck® GemTone Stain and ColorHard.
- Keeps soiling and contaminants from penetrating, making maintenance cleaning faster, more effective and more economical.
- Treated floors maintain slip resistance.
- Low odor. Easy to apply. Fast drying.
- UV stable. Will not yellow, discolor, peel or flake.
- VOC Compliant. Non-flammable. Non-toxic.
- Water-based.
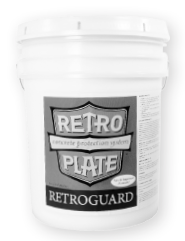
RetroGuard™
RetroGuard™ is a modified acrylic sealer yielding high reflectivity. The topical coating is suitable for protecting concrete surfaces against oil and food staining. It is highly effective at preventing acid staining, even keeping acidic fumes from the surface to which it is applied.
- Penetrating, long term protection. Won’t peel or flake.
- Protects surface from water and chemical attack.
- Ideal for all RetroPlate® treated floors – new or old, standard or colored.
- Enhances colored concrete, whether integrally colored or topically applied.
- Easy application. Low odor. No scrubbing or flushing required.
- Reduces maintenance.
- Complies with all known national, state and district AIM VOC regulations. Maximum VOC content 100 g/L
Sealers for Grind and Seal
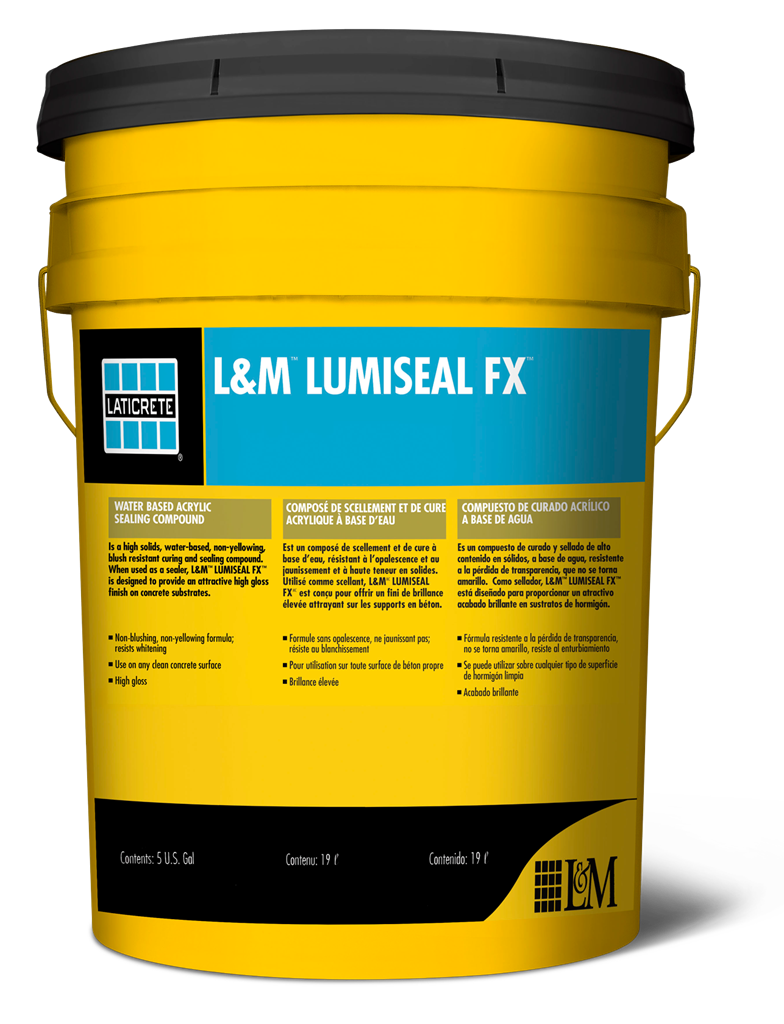
LUMISEAL FX™
LUMISEAL FX™ is a high solids, water-based, non-yellowing, blush resistant curing and sealing compound. When used as a sealer, LUMISEAL FX is designed to provide an attractive high gloss finish on concrete substrates. LUMISEAL FX is formulated with advanced low VOC, self-crosslinking emulsion chemistry, providing a very durable film and excellent early water-resistance to whitening or blistering. The durable film of LUMISEAL FX bonds easily to clean concrete surfaces and assures improved resistance to contaminants, stains, and abrasion. LUMISEAL FX offers superior protection when used over properly densified surfaces.
- Produces a long-lasting, tough protective shine on any interior concrete flatwork.
- Adds depth and luster to colored concrete.
- Keeps soiling and contaminants from penetrating, making maintenance cleaning faster, more effective and more economical.
- Treated floors maintain slip resistance.
- Low odor. Easy to apply. Fast drying.
- UV stable. Will not yellow, discolor, peel or
flake. - VOC Compliant. Non-flammable. Non-toxic.
Water-based.
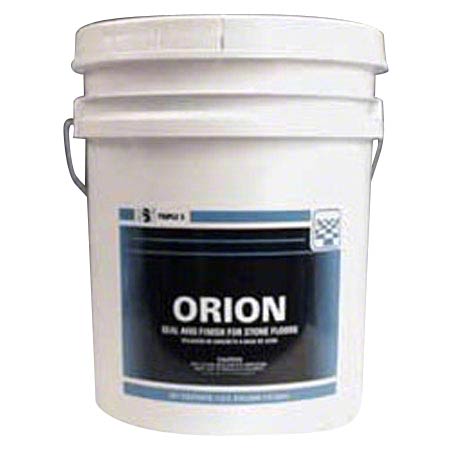
SSS Orion Seal & Finish
ORION is designed for the protection and maintenance of stone, concrete, terrazzo and natural tile flooring. Provides a barrier against soiled water, black marks, dusting, grease and other soils. Reduces maintenance and repair costs.
- Non-yellowing
- Water-based
- VOC compliant seal
- Protects floor, easier to clean, prevents dusting
- High solids